Jak prawidłowo zmierzyć czas cyklu?
Pojęcie czasu na produkcji ma niezwykłe znaczenie z punktu widzenia organizacji procesu produkcyjnego. Często jest jednym z głównych parametrów opisujących rzeczywistość, gdyż dzięki niemu wiemy dokładnie ile powinien trwać poszczególny proces lub jego etap. Czas jest także ważnym parametrem kontrolnym informującym czy procesy przebiegają prawidłowo, czy występują jakieś odchylenia od przyjętej normy. Wreszcie czas to ważne narzędzie służące do wartościowania pracy. Tym samym do powstania bazy służącej do wyceny produktu na poszczególnych etapach wytwarzania i wreszcie do wyceny gotowego produktu.
Prawidłowe zmierzenie czasu cyklu produkcyjnego należy rozpocząć od zrozumienia tego pojęcia i pojęć z nim związanych.
Cykl produkcyjny to powtarzalny czas upływający od momentu rozpoczęcia do zakończenia określonego etapu procesu produkcyjnego w danym miejscu w procesie poprodukcyjnym. Jest to czas, w którym operator/pracownik wytwarza na swoim stanowisku kompletny produkt. Kompletny z punktu widzenia wykonania wszystkich operacji przewidzianych dla jego stanowiska.
Okres cyklu produkcyjnego składa się z okresu roboczego i okresu przerw.
Czas roboczy to czas trwania operacji technologicznych, kontrolnych, konserwacji, transportu i magazynowania. Czas przerw to czas wynikających z organizacji procesu produkcyjnego jak np. w oczekiwaniu na zwolnienie stanowiska roboczego czy oczekiwania w magazynie oraz czas przerw wynikający z organizacji dnia roboczego jak np. planowe przerwy między zmianowe, przerwy śniadaniowe.
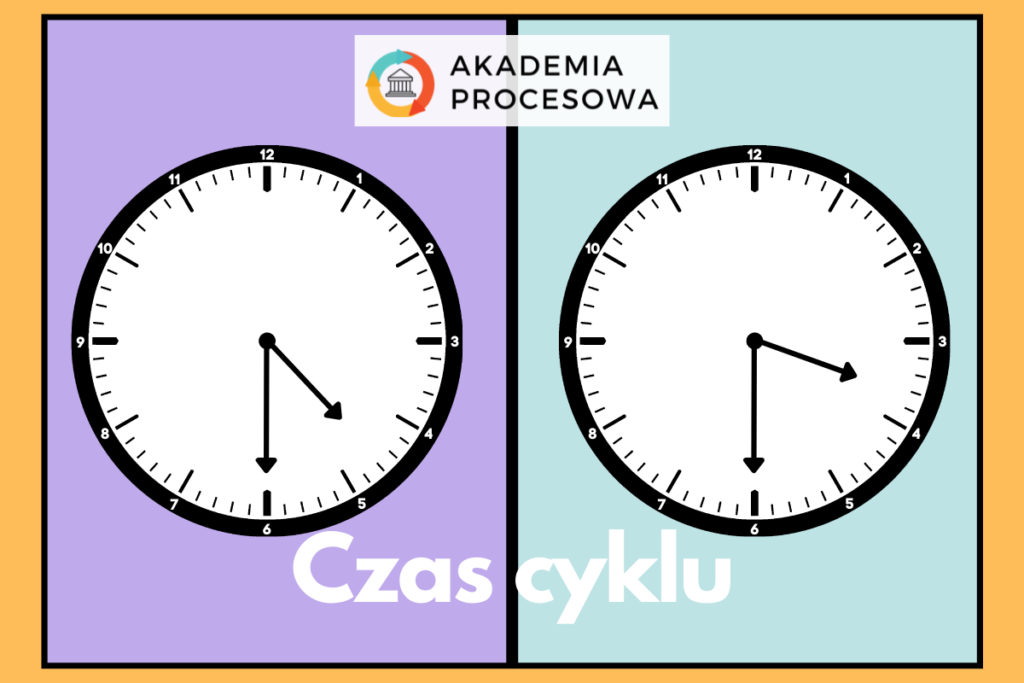
W jaki sposób wykonuje się pomiary czasu?
Najczęściej są to metody takie jak:
- Chronometraż– to metoda polegająca na obserwacji operacji i pomiaru jej czasu z użyciem najczęściej stopera oraz prowadzenia dokładnych notatek.
- Analiza ruchów elementarnych (MTM- Methods time measurement)– to przyporządkowanie czasów operacji zgodnie z sumą wszystkich ruchów elementarnych, które występują w danej czynności, a tym samym operacji. Zgodnie z tą metodą każdy ruch podstawowy ma swój własny określony czas trwania.
- Obserwacje migawkowe tzw. fotografia dnia– polegają na wyrywkowej, cyklicznej obserwacji stanowiska pracy. Metoda ta, należąca do technik statystycznych ma wskazać ile w losowo wybranych próbach czasowych znaleziono czasu dobrze spożytkowanego, a ile będącego marnotrawstwem.
Prawidłowy pomiar czasu cyklu, metodą chronometrażu, powinien być wykonany według następujących zasad:
- Ustalenie z pracownikiem daty i zasad pomiaru. Warto przygotować załogę na „akcję” pomiaru czasu, przede wszystkim po to, aby zminimalizować czynnik stresowy. Może wystąpić z naturalnych przyczyn i należy zapewnić w miarę możliwości naturalną pracę. Praktycznie każdy człowiek słysząc, że jego praca będzie wnikliwie analizowana i każda czynność będzie mierzona pod kątem długości trwania poczuje dyskomfort. Z tego też względu warto na samym początku wyjaśnić zasady i uspokoić pracownika. Ocenie i pomiarowi podgalają jedynie wykonywane czynności związane z produkowaniem wyrobu, a nie sam człowiek, jego styl pracy czy zachowanie. Wszelkie operacje powinny być wykonywane w normalnym codziennym, swobodnym tempie, tak jakby czas nie był mierzony.
- Osoba wykonująca pomiar powinna dokładnie umówić się z pracownikiem na termin pomiaru. Powinna przybyć w umówione miejsce chwilę przed czasem rozpoczęcia prac, tak aby pracownik nie zaczął sam wykonywać czynności wcześniej. Czas startu musi być jednakowy dla obu stron.
- Pracownik musi zostać powiadomiony o rozpoczęciu pomiaru, a osoba mierząca zarejestrować czas rozpoczęcia wykonywania czynności przez operatora. Czasami obserwacji stanowiska dokonuje się poprzez użycie kamery. Jest ona instalowana na czas pomiaru na stanowisku, a następnie zarejestrowany film podlega wnikliwiej analizie.
- Podczas pomiaru pracownik wykonuje tylko te czynności, które służą do wykonania jednego ustalonego egzemplarza produktu. Wszelkie czynności nie dające wartości dodanej do danego wyrobu muszą zostać usunięte z ostatecznego wyniku pomiaru.
- Wszelkie przerwy i przestoje, braki muszą zostać odnotowane przez mierzącego i skorygowane w ostatecznym wyniku. W końcowym wyniku pomiaru powinny znaleźć się tylko te, które mają ścisły związek z wytwarzanym przedmiotem.
- Do wykonania całego czasu cyklu muszą być zsumowane czasy wszystkich operacji. Chodzi tylko o te, które są potrzebne do wytworzenia kompletnego wyrobu, które są wykonywane na danym stanowisku roboczym.
- Pomiar czasu cyklu należy wykonać powtórnie innego dnia, na innej zmianie lub gdy operacje wykonuje inna osoba. Następnie należy obliczyć średnią z uzyskanych wyników. Aby próbka pomiaru była reprezentatywna dobrze jest powtórzyć wykonanie pomiaru czasu przynajmniej dziesięciokrotnie. Oczywiście jeśli cykl zamyka się w kilku, kilkunastu minutach. Jeśli jednak czas cyklu jest zdecydowanie dłuższy i osiąga nawet kilka godzin to warto powtórzyć pomiary w różnych sytuacjach. Przynajmniej dwa lub trzy razy.
- Bardzo często firmy produkcyjne do uzyskanego ostatecznego wyniku pomiaru czasu dodają tzw. parametr korygujący. Niweluje on niewielkie różnice wynikające z innego tempa pracy różnych osób.
- Analiza zmierzonego czasu cyklu powinna w sposób bardzo skrupulatny wyraźnie oddzielić czas, który jest związany z wykonywaniem operacji i jest jej nieodłączną częścią od tego, który nie powinien mieć miejsca. Chodzi tu o wyodrębnienie wszystkich niepotrzebnych czynności jak chodzenie, szukanie, oczekiwanie, dodatkowe przerwy. Zakłócają one sprawny przebieg procesu, gdyż nie są one wartością dodaną. W celu ułatwienia takiej analizy warto w zapiskach zamieszczać informacje przy danej czynności, czy jest ona wartością dodaną do operacji, czy zakłóceniem. Warto notować jakiego typu jest przerwa. Czy można jej uniknąć w przyszłości np. notoryczne szukanie narzędzi? Czy jest to czas technologiczny niezbędny w procesie (jak np. schnięcie kleju)? Szczegółowa analiza to podstawa do działań optymalizacyjnych.
Reasumując, czas cyklu produkcyjnego obrazuje w jakim czasie produkt przemieszcza się z jednego stanowiska pracy do drugiego, podczas wytwarzania kompletnego wyrobu. Pozwala wyznaczyć pewną normę czasową, stałą, służącą do kontrolowania prawidłowości przebiegu procesu oraz wartościowania wytwarzanego produktu.